Характерной особенностью и большим достоинством тонкопленочной технологии является возможность использования широкого набора материалов для получения пассивных элементов микросхемы с оптимальными характеристиками и почти любой конфигурации. При этом допуски на параметры элементов могут быть доведены до 1…2%, что особенно важно, когда точное значение номиналов и стабильность параметров имеют решающее значение. Современное технологическое оборудование и методы тонкопленочной технологии обеспечивают разрешающую способность рисунка микросхемы на порядок выше, чем при толстых пленках, что позволяет в 10 и более раз повысить уровень интеграции элементов в микросхеме. Упрощенная схема технологического процесса, приведенная на рисунке 2.37,б, отражает основные этапы производства и их взаимосвязь [25].
Расмотрим кратко содержание и особенности технологического процесса изготовления тонкопленочных элементов и микросхем широкого функционального назначения.
Получение тонкопленочных структур. Технологические методы получения тонко-пленочных структур базируются на использовании физических и химических процессов. Физические процессы составляют основу термического испарения в вакууме и катодного или ионно-плазменного распыления. На основе химических процессов разработаны следующие технологические методы: электрохимическое анодирование, гальваническое наращивание и осаждение из газовой фазы. Кроме того, в микроэлектронной технологии применяют иногда методики, для которых удачно сочетаются химичес
кие и физические процессы, например при катодном распылении в
реактивной среде, плазменном анодировании, термическом окислении.
Выбор метода реализации тонкопленочной структуры определяет
ся ее функциональным назначением и характеристиками, а также
технологичностью изготовления. При таком подходе наибольшее
распространение получили термическое испарение, катодное paс
пыление и электрохимическое наращивание. Значительно реже
применяют осаждение из газовой фазы и электрохимическое
наращивание. Однако в ряде специальных процессов эти методики, -
имеющие самостоятельное значение, широко используют (например, -
получение SiO2 из газовой фазы в полупроводниковой технологни и
глубокое анодирование в пленочной технологии cхем с многоуров-
невой разводкой).
Термическим испарением в вакууме получают пленки на устан
овках типа УВН, которые состоят из трех основных узлов: пульта
управления процессом (электрическая часть), системы откачки с ва
куумными агрегатами, рабочей камеры с подколпачным устрой-
ством для крепления и перемещения подложек и масок, а также для
нагрева подложек и исходного вещества. В рабочей камере с пo
мощью вакуумных агрегатов создают вакуум порядка 1,33×(
10-3…10-4) Па, затем, подавая напряжение от пульта управ-
ления, нагревают подложки и вещество, подлежащее напылению, до температуры его испарения. Образующийся поток пара конденсируется на подложке, температура которой значительно ниже температуры испарения материала.
Таким образом, процесс напыления тонких пленок можно paз-
делить на два основных этапа: формирование потока вещества и
конденсацию его в виде пленок на подложке. Чтобы обеспечить вы-
сокую воспроизводимость свойств пленок, необходимо в течение
всегo процесса с достаточно высокой точностью поддерживать oс-
новные технологические параметры: скорость осаждения, степень
вакуумирования и температуру подложки.
Заключительным этапом процесса напыления является термо
стабилизация пленок. Тер-мостабилизация заключается в выдержке подложки с напыленной пленкой при повышенной температуре и
постепенном охлаждении. В процессе термостабилизации снимаются
внутренние напряжения и упорядочивается структура пленок, что способствует улучшению электрофизи-ческих характеристик пленочных элементов и их стабильности во времени.
При катодном распылении молекулярный поток формируют,
распыляя материал с помощью газоразрядной плазмы. Для полу-
чения плазмы тлеющего разряда в вакуумной камере создают paзpя-
жение 1,33×(10-3...10-4) Па, после чего ее заполняют инертным газом
(чаще всего аргоном), давление которого устанавливают в пределах
1,33×(10...0,1) Па. При подаче к электродам высокого напряжения
возникает автоэлектронная эмиссия. Электроны, вырываемые с по
верхности катода электрическим полем, ионизируют инертный газ.
Положительные ионы инертного газа, ускоренные полем катода,
бомбардируют его, а при достаточной энергии распыляют катод.
Распыленные частицы, двигаясь направленно к поверхности -
подложки, оседают на ней и образуют пленку.
Метод катодного (или ионно-плазменного) распыления имеет
ряд достоинств. K числу которых относится возможность при срав
нительно низкой температуре получать пленки из таких
тугоплавких металлов, как вольфрам, молибден, тантал и др. ; получать пленки из сплавов, более однородные по составу и более равномер-
ные по толщине, чем при термическом испарении в вакууме. Адге-
зия пленок при ионном распылении лучше, и сами пленки имеют
состав, более близкий к составу исходного материала. Процесс
распыления практически безынерционен, режим распыления cpaв
нительно легко регулируется, и весь процесс в целом легче автома
тизировать, чем процесс термического испарения в вакууме.
Гальваническое осаждение (или электрохимическое наращивание)
основано на диссоциации солей металлов, растворенных в электро
лите, под действием тока и движения положительных ионов метал
ла к катоду, на котором помещена подложка. Данным методом в ос-
новном получают проводящие покрытия толщиной более 10 мкм.
Получение тонкопленочных микросхем. Пассивная часть тонкопленочных-
ГИС может состоять из резистивных микросхем, со-
держащих только резисторы, контактные площадки и коммутацион-
ные проводники, а также из резистивно-емкостных, содержащих
дополнительно многослойные пленочные конденсаторы.
Для создания резистивных и резистивно-емкостных микросхем
применяют танталовую технологию и термическое испарение в ва-
кууме в сочетании с процессами фотолитографии. Танталовая техно-
логия получила щирокое распространение в зарубежной практике. В странах СНГ
В ВВ чаще используют методы термического испарения
в вакууме. Ограниченное применение танталовой технологии обу-
словлено рядом существенных недостатков, связанных со слож-
ностью технологического процесса и низким значением удельного
сопротивления резистивных пленок на основе тантала и нитрида т
антала. Процесс изготовления резистивно-емкостных микросхем
по танталовой технологии предполагает использование разнородных методик: катодное распыление, термическое испарение, электрохимическое анодирование, и многократные процессы фотолито
графин. Кроме того, процесс характеризуется низкой технологичн
остью и высокой трудоемкостью. Простейшие микросхемы изго
тавливают термическим испарением в вакууме с применением метода
свободных масок. При повышении плотности элементов и усложне-
нии их конфигурации используют метод двойной фотолитографии.
Микросхемы с конденсаторами создают с применением метода
свободных масок, а в случае повышенной сложности – комбинирован-
ного метода. При этом резистивные и емкостные элементы формируют
напылением через маски, а проводящие элементы – с применением фотолитографии. Применение двойной фотолитографии в этом
случае ограничено растравливанием поверхности подложки при создании рисунка резистивных элементов, в результате чего снижается
как адгезия при напылении последующих слоев, так и надежность
микросхем в целом.
Для формирования резистивных элементов применяют металло-
силицидные сплавы и металлокерамические смеси. Резистивные ма-
териалы напыляют на подложки, нагретые до температуры не менее
250°С, непрерывно подавая порошки из вибробункера на ленточный
испаритель, нагретый до температуры 1800…1900 °C. Удельное
сопротивление резистивных пленок на основе металлосилициднык
сплавов составляет 50...3000 Ом·см, а на основе металлодиэлектри-
ческих смесей – 500...10000 Ом·см при толщине пленок не менее
0,03 мкм.
В качестве контактных площадок и коммутационных проводни-
ков используют пленки золота или алюминия с подслоем хрома и
ванадия, а также многокомпозиционные сплавы с разной температу-
рой испарения составляющих.
Конденсаторы формируют в виде многослойной структуры на
основе диэлектрических материалов: алюмосиликатного или боро
силикатного стекол, окиси германия или кремния. В качестве об
кладок конденсатора служат пленки алюминия, иногда с подслоем
титана. Удельная емкость такой структуры составляет 10-8…10-7
Ф/см2. Для повышения удельной емкости необходимо увеличить
число слоев в многослойной структуре. Однако выход годных и на
дежность конденсаторов при этом уменьшаются.
Для обеспечения прецизионных свойств пленочных микросхем
необходимо строго контролировать и поддерживать режимы нане-
сения пленок. Кроме того, для получения номинальных значений
элементов с точностью
1…0,1% необходимо предусмотреть спе-
циальные подстроечные элементы. Юстировку параметров элементов
выполняют различными способами: перепайкой или перерезанием
шин, удалением части рабочего слоя механическим путем или элект
ронным и лазерным лучами. Групповую подгонку номинальных зна-
чений сопротивлений резисторов осуществляют химическими
способами или терморегулирующим отжигом.
Получение микросхем с пересечениями. Оcновная трудность
создания микросхем с пересечениями заключается в получении
изолирующего слоя без сквозных пор, которые вызывают короткие
замыкания между коммутирующими элементами в процессе изro-
товления и эксплуатации микросхемы. Такие поры могут быть -
образованы, например, твердыми микроскопическими частицами, выбро
шенными из испарителя, дефектами на поверхности подложки, а также за счет локального распада конденсата и диффузии металли-
ческих частиц во время эксплуатации микросхем. Поры, загрязнения, неоднородности структуры подложки, ме-
ханические повреждения в изолирующем слое определяют относи-
тельно низкую надежность тонкопленочной многослойной комму-
тационной структуры. В связи с этим возникает необходимость новых технологических приемов и материалов, применение
которых обеспечивало бы изготовление бездефектной многослойной
коммутационной структуры. В настоящее время наиболее удачным, по-видимому
,следует считать технологический процесс изготовле
ния многослойной коммутационной структуры, в которой изолирую-
щим слоем служит полиимид.
Полиимиды являются термостойкими высокомолекулярными соединениями, не окисляются вплоть до температур
250…275 °C, допускают термообработку до 400 °С в течение нескольких часов без
значительных
изменений свойств. Применяя полиимид в качестве -
изолирующего слоя, можно построить два варианта технологичес
кого процесса. Первый вариант полностью основан на известных
методах тонкопленочной технологии. Во втором случае металлиза-
ция первого уровня представляет собой напыление, например, ме-
ди с подслоем хрома на подложку из ситалла и последующую фото
литографию. Затем методом центрифугирования наносят полиимид.
На высушенном слое полиимида методом фотолитографии вскры-
вают сквозные отверстия для межслойных переходов. Причем поли-
имид в окнах фоторезиста растворяют в гидрозингидрате. Чтобы
исключить образование сквозных отверстий в слое полиимида, операции
нанесения и формирования сквозных отверстий в слое полиимида
повторяются два, иногда даже три раза.
В принципе применение полиимида позволяет создавать тре-хуровневую коммутацию, однако из-за значительного усложнения
технологии и уменьшения числа выхода годных на практике огра
ничиваются двухслойной тонкопленочной коммутационной структурой.-
Весьма интересным технологическим решением является изго-
товление
двухслойной тонкопленочной коммутационной структуры на
основе готовой полиимидной пленки толщиной 50...60 мкм. Выруб
ленные из такой пленки заготовки промывают ацетоном от загряз
нений и высушивают в среде cyxoгo азота в течение нескольких -
часов. Затем на одну сторону пленки напыляют медь с адгезионным подслоем хрома. Во избежание деформации необходимо, чтобы при
напылении температура пленки нe превышала 50 °С. Выполнение
этого требования весьма важно, так как адгезия тонкой пленки к по
лиимидной подложке очень критична к напряжениям, возникающим
из-за разницы коэффициентов линейного pacтяжения тонкой напыленной пленки
металла и подложки. Отсюда ясно, что основной зa-
дачей при разработке технологии двухслойной структуры на по
лиимидной подложке является поиск таких условий металлизации, п
ри которых обеспечивается требуемая величина адгезии. Полиимидная подложка с тонкопленочной двухсторонней ком-
мутацией обеспечивает получение высокой плотности монтажа. В с
вязи с этим она находит применение там, где определяющим фак-
тором при выборе технологии является достижение выс-
окой плотности упаковки.
2.2.5. Сборка и герметизация ГИС
Сборка. Основным требованием к сборочно-монтажным процес
сам создания ГИС является обеспечение высокой плотностн мон
тажа и высокой надежности монтажных соединений, высокой про
изводительности и низкой стоимости.
Процесс сборки и монтажа сводится к установке бескорпусных активных элемен-
тов на подложку или коммутационную плату и подсоединению
внешних выводов этих элементов к пленочным контактным пло
щадкам. Метод монтажа в значительной степени определяется типом выводов активных элементов. В настоящее время наиболее ши-
рокое распространение получили бескорпусные микросхемы с про-
волочными, шариковыми (столбиковыми), балочными и паучковыми выводами (pиcунок 2.39). Соответственно и методы монтажа называют по типу выводов ИС: метод проволочного монтажа, метод перевернутого кристалла, метод балочных и паучковых выводов [15].
В таблице 2.10 даны сравнительные характеристики бескорпусных ИС,
применяемых в ГИС.
С точки зрения обеспечения отвода тепла (таблица 2.11) наилучшие характеристики имеет конструкция ИС с проволочными выводами.
В сочетании с эвтектической пайкой она обеспечивает минимальное
тепловое сопротивление. ИС с паучковой конструкцией
выводов
имеет такие же тепловые характеристики, что и ИС с проволочными выводами.Проволочная конструкция выводов, а также паучковая и балочная позволяют устранить основной недостаток проволочного монтажа –-
––––-------длорпро–––фывацук индивидуальную ручную сборку. При всех указанных методах монтажа, кроме метода перевернутого кристалла, имеется возможность визуально контролировать качество контактирования.
Наиболее простым вариантом сборки гибридных ИС является
сборка полупроводниковых ИС одной конструкции. Однако такой
вариант не всегда возможен: на одной подложке приходится совме-
щать несколько ИС с различной конструкцией выводов. В этом слу-
чае предъявляются повышенные требования к материалам подлож-
ки, проводящим пленочным покрытиям и материалу выводов.
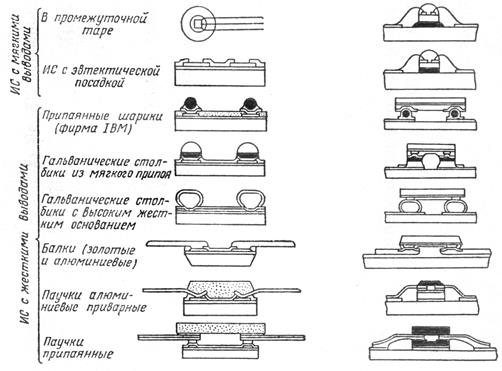
Рисунок 2.39 - Виды конструкций бескорпусных ИС
Наилучшим материалом для контактных площадок пассивных
плат является золото. Однако применение золота повышает стои-
мость микросборок, создает трудности в производстве и требует до-
полнительных мер для уменьшения его растворения в припое. До-
статочно широкое применение в качестве материала контактных пло-
щадок получило припойное покрытие. Полупроводниковые ИC
со столбиковыми и паучковыми выводами, покрытыми припоем, при
монтаже на припойные контактные площадки обеспечивают трехкратную их смену. Столбиковые (шариковые) выводы могут быть выполнены в двух
вариантах: выводы из чистого припоя и полужесткие выводы с ме
дным основанием, покрытым припоем. Конструкция с припойными
выводами из мягкого припоя является ненапряженной и нежесткой.
Она обеспечивает высокую надежность соединения и, в частности,
устойчивость соединения к циклическим воздействиям температу-
ры. Однако технология изготовления пассивной части для мон-
тажа ИС с выводами из припоя достаточно сложна. Это связано с не-
обходимостью иметь изолированные контактные площадки разной
площади.
На качество монтажа ИС с полужесткими выводами влияет разн-
овысотность контактных площадок, материал и класс обработки
поверхности подложки, число выводов ИC. Толстопленочная техно-
логия обеспечивает разновысотность в пределах одной группы
контактных площадок около 10...12 мкм, вакуумные методы напы-
ления – не более 0,5 мкм даже при толщине слоя 6...10 мкм. До
пустимая разновысотность контактных площадок около 5 мкм, по
этому контактные площадки, полученные трафаретной печатью,
требуют применения методов выравнивания.
В качестве материала припойного покрытия применяют обычно олово с добавками висмута (0,5%). Поскольку этот материал не смачивает диэлектрическую подложку и не имеет к ней адгезии,то приходится последовательно напылять хром, никель, олово. Напылением через маски нетрудно получить проводники с шириной и зазором между ними по 150 мкм. Толщины напыленных слоев никеля и олова зависят от класса обработки поверхности. Важно, чтобы максимальная толщина олова была всегда больше максимальной неровности подложки. Для подложек, имеющих 7-й класс чистоты обработки поверхности, наилучшие значения выхода годных получаются при толщине никеля не менее 0,3 мкм и толщине олова не менее 8 мкм. Одним из факторов, определяющих надежность контактирования с полужесткими столбиковыми выводами, является согласованность
коэффициентов линейного расширения кремния и диэлектрической
подложки. Чем больше число выводов и больше разница коэффи-
циентов, тем меньше устойчивость соединения к циклическому воз-
действию тепла в интервале температур эксплуатации.
Таблица 2.10
Вид конструкции
|
Вид защиты
|
Технологичность
монтажа
(автомат)
|
Ремонтопригодность
|
Удобство обращения
при монтаже
|
Мягкие
выводы
| ИС в таре
ИС с эвтектической
посадкой
| Неорганическая
и органическая
То же
| Низкая
-
| Средняя
Низкая
| Хорощее
Среднее
|
Шариковые
и столбико
вые выводы
|
Шариковые
ИС с мягким припоем
ИС с большим
твердым
основанием
|
Неорганическая
-
-
|
Хорошая
-
-
|
Хорошая
-
-
|
Хорошее
-
-
|
Жесткие
консольные
выводы
| Балка
Алюминиевые
Припойные
| -
-
То же и органическая
| -
-
-
| Средняя
Низкая
Хорошая
| Среднее
Хорошее
-
|
Надежность
соединений
| Способность
рассеивания тепла
| Плотность
упаковки
| Пригодность к автомати
зации измерительных
операций
| Температурный
диапазон монтажа
|
Низкая
-
| Средняя
Хорошая
| Средняя
-
| Средняя
Низкая
| Ограничен предельной температурой органической
защиты
То же
|
Высокая
-
-
|
Средняя
-
-
|
Высокая
-
-
|
Средняя
-
-
| Ограничен температурой
припоя
То же
Допускает кратковременные
воздействия температурой
до 500 °С
|
Хорошая
-
-
| Средняя
Средняя (хорошая при электромонтаже )
То же
| Средняя
Средняя
(низкая)
То же
| Хорошая
Хорошая
(в ленте)
То же
| То же
-
Ограничен предельной температурой органической защиты и температурой припоя
|
Таблица 2.11
Конструкция ИС
| Тепловое сопротивление, °С/Вт
|
подложки
| выводов
| кремния
| суммарное
|
Проволочные выводы с эвтектической посадкой
Балочные выводы
Столбиковые выводы
|
|
-
35 (при 36 выводах)
0,2 (при 36 выводах)
|
|
|
Применение толстых пленок для получения наружного слоя
коммутации в гибридных БИС позволяет комплектовать их много
выводными (более 4-x) полупроводниковыми ИС с проволочными,
паучковыми, балочными выводами. Тонкопленочная коммутация не ограничивает применение полупроводниковых ИС с различными конструкциями выводов.
В процессе сборки бескорпусные ИС крепят на плате с помощью
эпоксидных компаундов или эвтектических сплавов. В первом слу-
чае переход активный элемент – плата является электроизоля
ционным, во втором случае – омическим. Чаще всего применяют ком-
паунд на основе эпоксидной смолы ЭД-6. Выбор этого компаунда
обусловлен его высокой адгезией к различным материалам, малой
усадкой при отвердевании, химической стабильностъю. Подбирая
отвердители, эпоксидным компаундам можно придать различные
физические и технологические свойства: высокую теплопровод-
ность, желаемые коэффициент линейного расширения, рабочую температуру, малую степень усадки и требуемую эластичность. При эвтектическом спае на подложку в нужном месте наносят
слой золота толщиной в несколько микрометров, на который и по-
мещают полупроводниковую ИС. Затем подложку с микросхемой
разогревают до температуры, несколько превышающей температуру
эвтектики кремний - золото (370 °С). При такой температуре и
некотором равномерном давлении на кристалл взаимно растворяют
ся кремний и золото и образуется эвтектический спай на границе
раздела. Если толщина пленки золота мала, то между ней и кри-
сталлом помещают таблетку эвтектического сплава толщиной 10...
20 мкм.
Мягкие проволочные выводы ИС подсоединяют к контактным
площадкам чаще термокомпрессионной или ультразвуковой
сваркой. В таблице 2.12 отражены методы монтажа, получившие ши-
рокое распространение в производстве гибридных БИС.
Термокомпрессионная сварка основана на одновременном воз
действии на свариваемые участки повышенной температуры и дав-
ления. Уровень давления подбирают таким образом, чтобы про-
водник деформировался только после его разогрева. Давление
0,1...0,6 кг передается через сварочный инструмент. Место сварки
нагревают тремя способами: специальным подогревателем (paзo-
грев всей подложки), подогретым сварочным инструментом или
подсоединяемой проволокой, через которую пропускает импульс
тока в месте контакта. Режимы термокомпрессионной сварки не
критичны и могут изменяться в достаточно широких пределах. Существенными недостатками термокомпрессионной cвapки яв-
ляется трудность ее автоматизации и сравнительно невысокая проч-
ность свариваемого соединения. Более перспективной является
ультразвуковая (УЗ) сварка, обеспечивающая лучшее качество сое-
динений, разнородных по составу и толщине. Достоинством УЗ сварки также является возможность ее выполнения групповым методом.
Meтод ультразвуковой сварки основан на одновременном воз
действии колебаний ультразвуковой частоты, возбуждаемых в сва
риваемых деталях, и давления в области сварки. Под действием
продольных УЗ колебаний разрушается окисная пленка контакти-
рующих поверхностей, обнажаются чистые слои металлов. В pe
зультате давления и ультразвуковых вибраций в месте контакта
происходит металлургическое сращивание соприкасаемых поверх-
ностей. Образуется довольно прочное соединение. Современные промышленные установки для ультразвуковой сварки снабжены устройствами перемещения инструмента, свариваемой проволоки и столика с микросхемой.
Таблица 2.12
Конструкция
выводов
|
Материал выводов
| Методы монтажа полупроводниковых ИС при разных материалах контактных площадок пассивной платы
|
Олово - висмут
| золото
| алюминий
|
Проволочная
|
Алюминий
Алюминий или медь,
покрытые припоем
|
-
-
КН
РЭ
|
УЗ
КН+УЗ
КН
РЭ
УЗ
|
КН+УЗ
УЗ
-
-
|
Паучковая
|
Алюминий
Медь (никель),
покрытые припоем
|
-
КН
РЭ
|
РЭ
УЗ+КН
КН
|
УЗ
РЭ
|
Балочная
|
Алюминий
Золото
|
-
-
|
КН
РЭ
УЗ+КН
КН
РЭ
|
УЗ+КН
КН
РЭ
УЗ
|
Столбиковая
|
Припой
Медь
Алюминий
Золото
| Пайка припойными пастами в печи или при помощи локального
импульсного нагрева подложки
|
КН
УЗ+КН
КН
УЗ+КН
-
| КН
УЗ+КН
КН
УЗ+КН
УЗ+КН
| -
КН
УЗ+КН
УЗ+КН
|
Примечание 1. Пpи всех методах монтаж на керамических подложках выполняют с их подогревом до 150…200 C.
Примечание 2. KH-сварка или пайка импульсным косвенным нагревом; РЭ - сварка и пайка расщепленным (сдвоенным, строенным ) электродом; УЗ – сварка или пайка при воздействии ультразвуковых колебаний.
Герметизация. В реальных условиях эксплуатации микросхемы
подвергаются воздействию различных факторов (тепла, влаги, аг-
рессивных химических сред и т. п.), серьезно влияющих на их ра-
ботоспособность и надежность. Для защиты от внешних воздействий
микросхемы герметизируют. Степень необходимой герметизации
и ее способы зависят от назначения микросхем и области их приме
нения, материалов микросхем, герметизирующих материалов, уров-
ня развития технологии и зкономических соображений.
По конструктивно-технологическим признакам герметизация
разделяется на бескорпусную и корпусную. Бескорпусную герме-
тизацию выполняют в основном заливкой микросборок в специаль-
ные заливочные формы. Герметизацию производят в вакуумной ка-
мере или при небольшом избыточном давлении. В качестве зали-
вочных материалов применяют: эпоксидные, кремнийорганические
и полиуретановые компаунды, а также полиэфиры и полисульфиты.
Наибольшее распространение получили компаунды с различными
наполнителями, обеспечивающими необходимые физические и тех-
нологические свойства: механическую прочность, теплопроводность,
эластичность и пр. При бескорпусной герметизации масса и габа-
риты приблизительно в 1,5 раза, а стоимость примерно на 30% мень-
ше, чем при корпусной. Однако бескорпусная герметизация, как
и защита пластмассовыми корпусами, не обеспечивает надежной
защиты микросхем от влаги. Дело в том, что даже в условиях нор-
мальной влажности на поверхности защитного слоя микросхемы
всегда имеется пленка воды толщиной около 0,01 мкм. А так как
диаметр молекул воды значительно меньше размеров микропор и
микротрещин защитных материалов, то проникновение влаги под
защитный слой со временем неминуемо. И хотя этот процесс проте-
кает очень медленно, со временем под защитной пленкой накапли-
вается влага. Как известно, вода – химически активное вещество,
способствующее образованию солей, щелочей, кислот. Поэтому
появление под герметизирующим слоем воды приводит к образованию там концентрированного водного раствора солей. Так как
с внешней стороны пленки раствор солей менее концентрированный,
создаются условия для интенсивного проникновения влаги под
пленку. В результате под пленкой возникает значительное давление,
приводящее к вспучиванию и отслаиванию защитного слоя. Поэтому
для микросхем более надежным способом защиты от влаги является
вакуум-плотная герметизация с использованием специальных корпусов-
. В зависимости от материала, применяемого для изготовления корпусов, и способа герметизации их внешних выводов вакуум-плотные корпуса подразделяют на стеклянные, металлостеклянные,
металлические, керамические и металлокерамические.
Для герметизации толстопленочных ГИС применяют в основном металлические, керамические и металлокерамические корпуса.
Металлические корпуса штампуют из алюминиевого сплава, а затем анодируют для придания им декоративного вида. Для герметизации толстопленочные микросхемы устанавливают в анодированный корпус и заливают эпоксидным компаундом со стороны штырей (выводов).
Керамические и металлокерамические корпуса, как и металлостеклянные, состоят из двух частей – основания и крышки. Основание корпуса изготавливают из вакуум-плотной алюмосиликатной керамики или окиси бериллия,
характеризующихся повышенной стойкостью к термо-ударам, а крышку – либо из этой же керамики,
либо из металла. При герметизации в металлоке-рамическом корпусе коэффициенты линейного расширения материалов крышки и осно-
вания должны быть одинаковыми. Обычно металлическую крышку
изготавливают из ковара, никеля, меди. Чтобы обеспечить прочное
соединение крышки с керамическим основанием, плоскости их кон-
тактирования металлизируют молибдено-марганцевой пастой с по-
следующим осаждением слоя никеля или меди. Крышку припаивают к основанию серебряным припоем.
Качество герметизации определяется скоростью натекания газов
из внешней среды. Герметичность проверяют масс-спектрометри-
ческим методом с помощью гелиевого течеискателя.