Традиционные процессы прессования классифицируют по следующим основным признакам:
1) по направлению истечения металла — прямое и обратное;
2) по температуре обрабатываемого металла — холодное и горячее;
3) по наличию внутреннего канала — сплошных профилей и полых с применением иглы (для труб) и матриц со сварочными камерами;
4) по использованию смазки — со смазкой и без смазки.
Также известны усовершенствованные процессы:
1) гидропрессование;
2) с активным действием сил трения; 3) полунепрерывное и непрерывное; 4) метод Conform и др.
Рассмотрим сущность перечисленных способов прессования.
При п р я м о м п р е с с о в а н и и (рис. 6.4)[22] направление действия силы прессования Р совпадает с направлением течения
Рис. 6.4. Схема прямого прессования:
|
1 — контейнер; 2 — матрица; 3 — матрицедержатель; 4 — пресс-шайба; 5 — прессштемпель; 6 — пруток; 7 — передняя поперечина пресса;
a— первичная зона пластической деформации; б — вторичная зона деформации; в — подверженная влиянию трения поверхностная зона; г — «мертвая» зона; д — недеформируемая зона; Р — сила прессования; v — cкорость течения металла
При этом металл движется относительно неподвижного контейнера, возникают напряжения трения в приконтактном слое в, что приводит к росту силы прессования. На рис. 6.4 показана схема волочения через плоскую матрицу, что допустимо при прессовании пластичных (например, алюминиевых) сплавов. При этом возникает воронкообразная «мертвая» зона г, которая выполняет функции входного конуса матрицы, а пластическая деформация сосредоточена только в области а. Высота пресс-остатка в конце прессования составляет примерно 1/6 диаметра контейнера[23].
Прямое прессование прутков может осуществляться в холодном состоянии со смазкой, в горячем состоянии со смазкой и без смазки с «рубашкой» и без «рубашки».
Рассмотрим операции прессования прутка в горячем состоянии без смазки с «рубашкой» (рис. 6.5), например прессование медных сплавов. «Рубашка» — это отслой из загрязненных и окисленных наружных слоев осаженной в контейнере заготовки, который после прессования остается на стенках контейнера и должен быть удален. Для образования «рубашки» между контейнером и прессшайбой создают зазор 2—3 мм. Преимущества прессования с «рубашкой» заключаются в том, что загрязненные и окисленные наружные слои не попадают в готовое изделие, а удаляются. Технологический процесс прессования (см. рис. 6.5) содержит операцию отделения «рубашки» с помощью очистного диска, для чего после прессования контейнер отводится назад, чтобы обеспечить использование втулки для отделенной рубашки и инструментов между матрицей и контейнером (во втулке оказываются очистной диск, рубашка, пресс-шайба и пресс-остаток). Прессование в этом случае включает стадии, указанные на рис. 6.5.
Прямое прессование стальных прутков осуществляется в горячем состоянии со смазкой. В качестве смазки используется стекло, для этого в исходном состоянии между передним торцом заготовки и дном контейнера помещается стеклянный диск. В процессе прессования стекло размягчается и обеспечивает хорошее смазывающее и одновременно изолирующее действие (сохранение тепла заготовки).
Так как в этом способе прессования поверхность прутка образуется из наружных зон заготовки, ее подвергают обточке или другой поверхностной обработке для удаления поверхностных дефектов.
Прямое прессование прутков в холодном состоянии из пластичных сплавов (например, алюминия) осуществляется через коническую матрицу со смазкой (рис. 6.6). Для облегчения прессования торец заготовки обтачивают на конус. Прессование включает стадии, указанные на рис. 6.6.
Рис. 6.5. Стадии прессования (
|
а
1 — контейнер; 2 — матрица; 3 — матрицедержатель; 4 — пресс-шайба; 5 — пресс-штемпель; 6 — заготовка; 7 — передняя поперечина пресса; 8 — пила; 9 —
«рубашка»; 10 — очистной диск; 11 — пресс-остаток; 12 — втулка приспособления для удаления «рубашки» и инструмента;
а — исходная позиция; б — распрессовка и прессование до достижения заданной величины пресс-остатка; в — отвод контейнера, отрезка прутка и введение очистного диска для удаления рубашки (слева); г — выталкивание из контейнера очистного диска, рубашки, пресс-шайбы и пресс-остатка в специальную втулку; д — вывод втулки приспособления с содержимым, возврат в исходную позицию
Рис. 6.6. Стадии прессования (а—г) прутка в холодном состоянии со смазкой:
1 — контейнер; 2 — матрица; 3 — матрицедержатель; 4 — пресс-штемпель с прикрепленной к нему пресс-шайбой; 5 — исходная заготовка с коническим торцом;
6 — передняя поперечина пресса; 7 — нож; 8 — манипулятор; а — исходная позиция; б — распрессовка заготовки в контейнере; в — прессование до достижения заданной величины пресс-остатка; г — отвод контейнера и пресс-штемпеля, удаление пресс-остатка с помощью пилы и манипулятора, отрезка пресс-изделия
При о б р а т н о м п р е с с о в а н и и (рис. 6.7)[24] направление действия силы прессования Р противоположно направлению течения металла со скоростью v.В этом способе практически отсутствует скольжение металла по контейнеру, поэтому сила прессования значительно меньше. Для обеспечения движения металла против направления приложения силы прессования Р пресс-штемпель выполняют пустотелым.
Рис. 6.7. Схема обратного прессования прутка:
|
1 — контейнер; 2 — матрица; 3 — заготовка; 4 — затворный пресс-штемпель;
5 — пустотелый матричный пресс-штемпель; 6 — пруток; 7 — зона пластической деформации
Обратное прессование имеет следующие п р е и м у щ е с т в а перед прямым:
— меньшее усилие прессования, возможность снижения температуры заготовки (при горячем прессовании) и увеличения коэффициента вытяжки;
— более высокое качество изделий;
— более высокая производительность процесса;
— меньшая неравномерность деформации по сечению и большая скорость прессования;
— больший выход годного за счет уменьшения длины прессостатка до 1/10 от диаметра контейнера;
— увеличение срока службы контейнера из-за отсутствия подвижного контакта с заготовкой.
Обратное прессование применяется для производства проволоки, прутков и профилей чаще всего из алюминия, его сплавов, а также латуни, в том числе труднодеформируемой. Для прессования сталей обратное прессование, как правило, не применяется[25].
Известны следующие р а з н о в и д н о с т и о б р а т н о г о п р е с с о в а н и я прутков:
— в горячем состоянии без смазки без «рубашки»;
— в горячем состоянии без смазки с «рубашкой»;
— в холодном состоянии без смазки и без «рубашки»;
— в холодном состоянии со смазкой без «рубашки» (см. рис. 6.7).
В последнем случае в контейнер задается покрытая смазкой заостренная заготовка, а прессование (например, алюминия) осуществляется через коническую матрицу.
Для п р е с с о в а н и я т р у б используется дополнительный инструмент — игла (оправка). Исходная заготовка может быть сплошной (тогда прессованию предшествует прошивка заготовки) и с просверленным отверстием. Во время прессования необходимо преодолеть силы трения на контакте иглы с заготовкой, поэтому сила прессования возрастает по сравнению с прессованием прутков.
Прямое прессование труб может осуществляться в следующих вариантах:
1) в горячем состоянии с неподвижной и подвижной иглой; 2) в холодном состоянии с неподвижной иглой.
На рис. 6.8[26] изображена схема горячего прессования трубы из предварительно просверленной заготовки из алюминиевого сплава с неподвижной иглой. Диаметр отверстия заготовки, как правило, немного меньше диаметра иглы, которая имеет заостренный конец. Для расширения отверстия применяется экспандирование.
Отверстие в заготовке обеспечивает направленное движение иглы; пресс-штемпель, внутри которого расположена игла, выполняется пустотелым. После достижения заданной длины пресс-остатка игла, пресс-штемпель и контейнер отводятся назад, чтобы отделить пресс-остаток ножницами.
Рис. 6.8. Схема прямого прессования труб с неподвижной иглой:
1 — контейнер; 2 — матрица; 3 — матрицедержатель; 4 — пресс-шайба; 5 — прессштемпель; 6 — игла; 7 — труба
В другом варианте процесса подвижная игла не имеет заостренного конца и может двигаться со скоростью пресс-штемпеля, будучи закрепленной в нем, за счет чего снижаются силы трения и сила прессования. Также игла может двигаться быстрее прессштемпеля, способствуя движению металла.
Обратное прессование труб осуществляется в горячем состоянии в следующих вариантах:
— с неподвижной иглой со смазкой и без смазки иглы; — с подвижной иглой со смазкой и без смазки иглы.
На рис. 6.9 изображена схема одного из вариантов процесса обратного горячего прессования трубы без смазки с неподвижной иглой (например, алюминиевого сплава).
Приг и д р о с т а т и ч е с к ом п р е с с о в а н и и (рис. 6.10)[27]металл выдавливается из контейнера не с помощью пунсона, а жидкостью высокого давления. Процесс осуществляется главным образом в холодном состоянии, горячее прессование применяется для прессования труднодеформируемых сталей и сплавов. В качестве гидростатической среды чаще всего используется рициновое (касторовое) масло, хотя известно использование твердых
Рис. 6.9. Обратное прессование труб с неподвижной иглой:
1 — контейнер; 2 — матрица; 3 — затворный пресс-штемпель; 4 — игла; 5 — пустотелый пресс-штемпель; 6 — держатель пустотелого пресс-штемпеля; 7 — передняя поперечина пресса; 8 — заготовка; 9 — труба
Рис. 6.10. Схема гидростатического прессования:
|
1 — контейнер; 2 — матрица; 3 — заготовка; 4 — гидростатическая среда; 5 — прессштемпель; 6 — пруток; 7 — уплотнения
и газообразных рабочих сред. Необходимое давление жидкости в контейнере создается либо под действием перемещения плунжера, либо подачей в контейнер извне (например, через центральное отверстие пресс-штемпеля). Таким способом прессуются чаще всего изделия из алюминиевых и медных сплавов в холодном состоянии, реже — стальные профили и трубы. Главным преимуществом гидростатического прессования является отсутствие контакта заготовки со стенками контейнера и сил трения на контактных поверхностях, что существенно повышает однородность деформации по сечению и качество поверхности изделия.
Недостатки гидропрессования связаны с большой стоимостью специализированных прессов и инструмента, а также значительной скоростью выталкивания пресс-изделий при переходе потенциальной энергии сжимаемой жидкости в кинетическую энергию прессизделия. Последнее обстоятельство вызывает необходимость установки специальных тормозов для исключения смятия изделия. Поэтому широкого промышленного применения этот процесс пока не нашел.
П р е с с о в а н и е с а к т и в н ы м д е й с т в и е м с и л т р е н и я (рис. 6.11) обеспечивается за счет одновременного движения контейнера с большей скоростью vк , чем скорость пресс-штемпеля vп и металла, в сторону матрицы. В результате контейнер увлекает за собой контактные слои заготовки, что облегчает прессование и способствует выравниванию скоростей течения металла по сечению заготовки, улучшению структуры, уменьшению величины пресс-остатка и вероятности пресс-утяжин.
Наибольший эффект этого вида прессования достигается при полном прилипании металла к контейнеру: например, при прессовании алюминиевых сплавов без смазки, а также при прессовании труб с подвижной иглой. Одним из недостатков прессования с подвижным контейнером является необходимость привода перемещения контейнера в прессовой установке.
Рис. 6.11. Схема прессования с активным действием сил трения
П о л у н е п р е р ы в н о е п р е с с о в а н и е( рис. 6.12) нацелено на повышение выхода годного изделия и производительности, для этого пресс-остаток от прессования предыдущей заготовки используют для дальнейшего прессования «след в след».
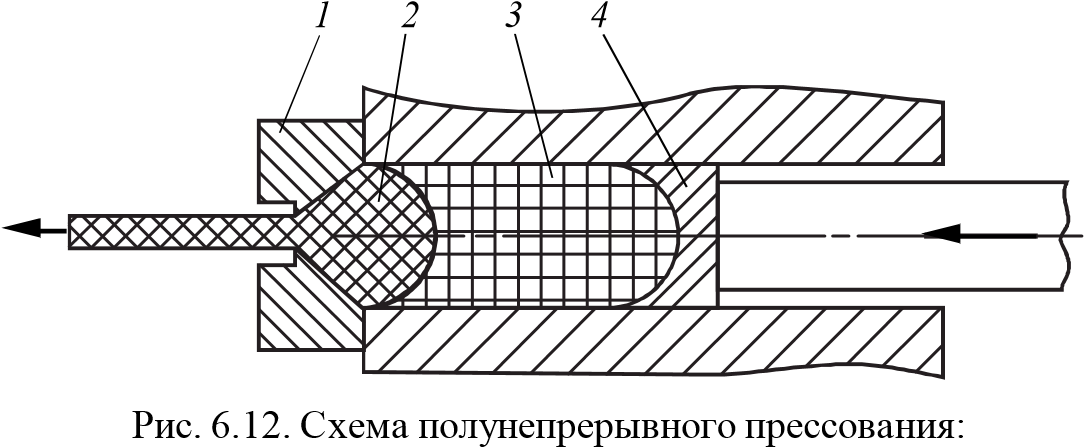
1 — матрица; 2 — прессуемая заготовка; 3 — следующая заготовка; 4 — вогнутая пресс-шайба
В процессе прессования пресс-остаток сваривается со следующей заготовкой, поэтому этот процесс чаще ведется без смазки с подогревом контейнера. Для лучшей сварки торцевых поверхностей используют вогнутую пресс-шайбу (рис. 6.12, 4), что обеспечивает выпуклую поверхность стыка, увеличивая ее площадь и, как следствие, прочность сваренного соединения. Полунепрерывным прессованием получают алюминиевую проволоку, шины для электропромышленности, осуществляют наложение свинцовой или алюминиевой оболочки на электрические кабели и т. п.
Н е п р е р ы в н о е п р е с с о в а н и епозволяет получать изделия большой длины за счет непрерывной подачи заготовки в канал матрицы (рис. 6.13). Для реализации процесса можно использовать различные принципы: гидропрессования (рис. 6.13, б) , механической подачи с помощью задающих роликов (рис. 6.13, а) , гусеничных траков (рис. 6.13, в) и др.
При этом виде прессования значительно повышаются выход годного изделия (за счет отсутствия пресс-остатков единичных заготовок) и производительность (ввиду экономии времени на перезарядку контейнера и замену инструмента). Кроме того, непрерывность процесса обеспечивает стабильность получаемых свойств
изделий и возможность применения непрерывно-литой заготовки.
|
Рис. 6.13. Схемы непрерывного прессования с использованием различных способов (а—в) подачи заготовки :
1 — прессуемый металл; 2 — матрицы; 3 — задающие органы; а — подача задающими роликами; б — с жидкостью высокого давления; в — бесконечной лентой гусеничных траков
М е т о д C o n f o r m (рис. 6.14) разработан в 1971 г. в Англии и представляет собой разновидность непрерывного прессования. Непрерывная подача заготовки в матрицу осуществляется с помощью силы трения от вращающегося экструзионного колеса, которое имеет по периметру желоб, соответствующий форме сечения исходной заготовки (прутка). Желоб уплотнен замыкающим элементом снизу, а выход из желоба закрыт затворным элементом сверху так, что течение металла возможно только через матрицу, установленную, чтобы обеспечивать тангенциальный (вверх) или радиальный (как показано на рис. 6.14) выход изделия (проволоки). Метод Conform применяется для прессования малопластичных сплавов с высокими коэффициентами вытяжки; прессования гранулированных и порошковых материалов; в комбинации с литьем, для чего жидкий металл заливается непосредственно в желоб экструзионного колеса, а также нанесения кабельной оболочки.
6.3. Технологические схемы производства
Рис. 6.14. Схема прессования по методу Conform:
|
1 — экструзионное колесо; 2 — замыкающий элемент; 3 — затворный элемент;
4 — матрица; 5 — заготовка (пруток); 6 — прессуемое изделие (проволока)